13 | GEOBI TWO-COMPONENT GROUTING MORTAR
Geopietra® has created the innovative GeoBi two-component mortar (dry/wet) which is ideal for finishing off Geopietra® manufactured stone veneer and brick wall coverings, and is suitable for indoors and outdoors. All GeoBi colours selected from typical soils and mortars in Europe have been standardised for use with various Geopietra® models and shades.
GeoBi two-component mortar is available in 6 colours: SABBIA, MARCHE, TOSCANA, GRIGIO CIELO, GRIGIO and ARENA and 2 grain sizes: fine grain 0-3 mm and coarse grain 3-8 mm. Thanks to its versatility it meets the most varied aesthetic requirements, ranging from rustic charm to smooth textures. GeoBi mortar has ideal flow characteristics for injecting joints using a piping bag. At the right consistency it doesn’t drip and dirty the stone, doesn’t shrink and crack when drying, and adheres perfectly to stone walls and bases. Traditional mortars or other ready-mixed products are not suitable.
PREPARATION
Mix GeoBi/A coloured mortar with 4.3-4.8 Lt of clean cold water for each 25-kg bag and create a smooth paste. Then add GeoBi /B volcanic aggregate in a ratio of 1:1 (7.5-lt bag) and mix until a smooth paste is obtained. Wait for approximately 10 minutes then mix again; processing time depends on temperature. With summer temperatures and very absorbent bases keep it at a fairly liquid consistency, and at a thicker consistency in winter temperatures (no lower than 5°C).
CAUTION: using material which is dry or comes from bags left open is problematic when handling the grout due to the prolonged absorbency of the aggregate.

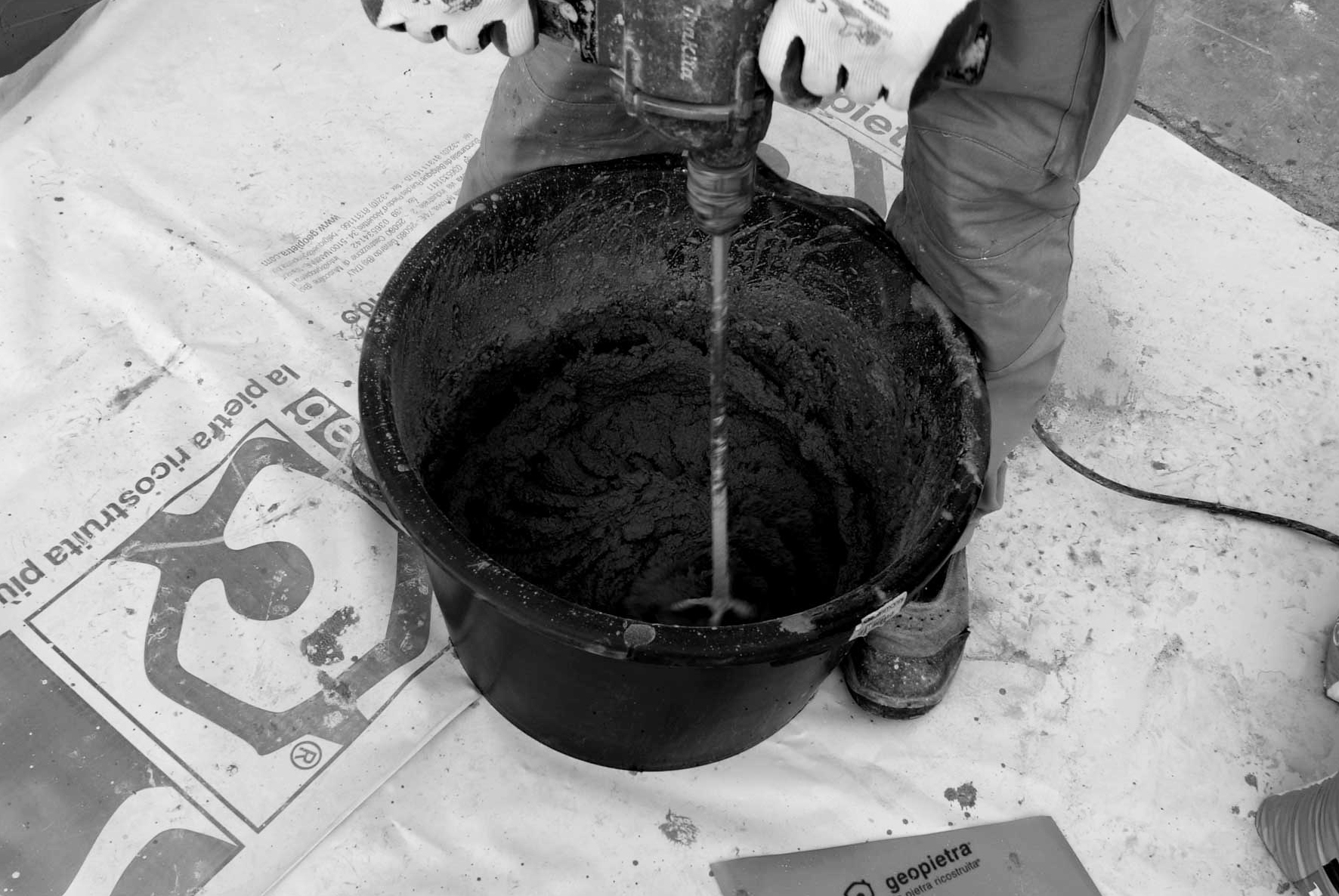
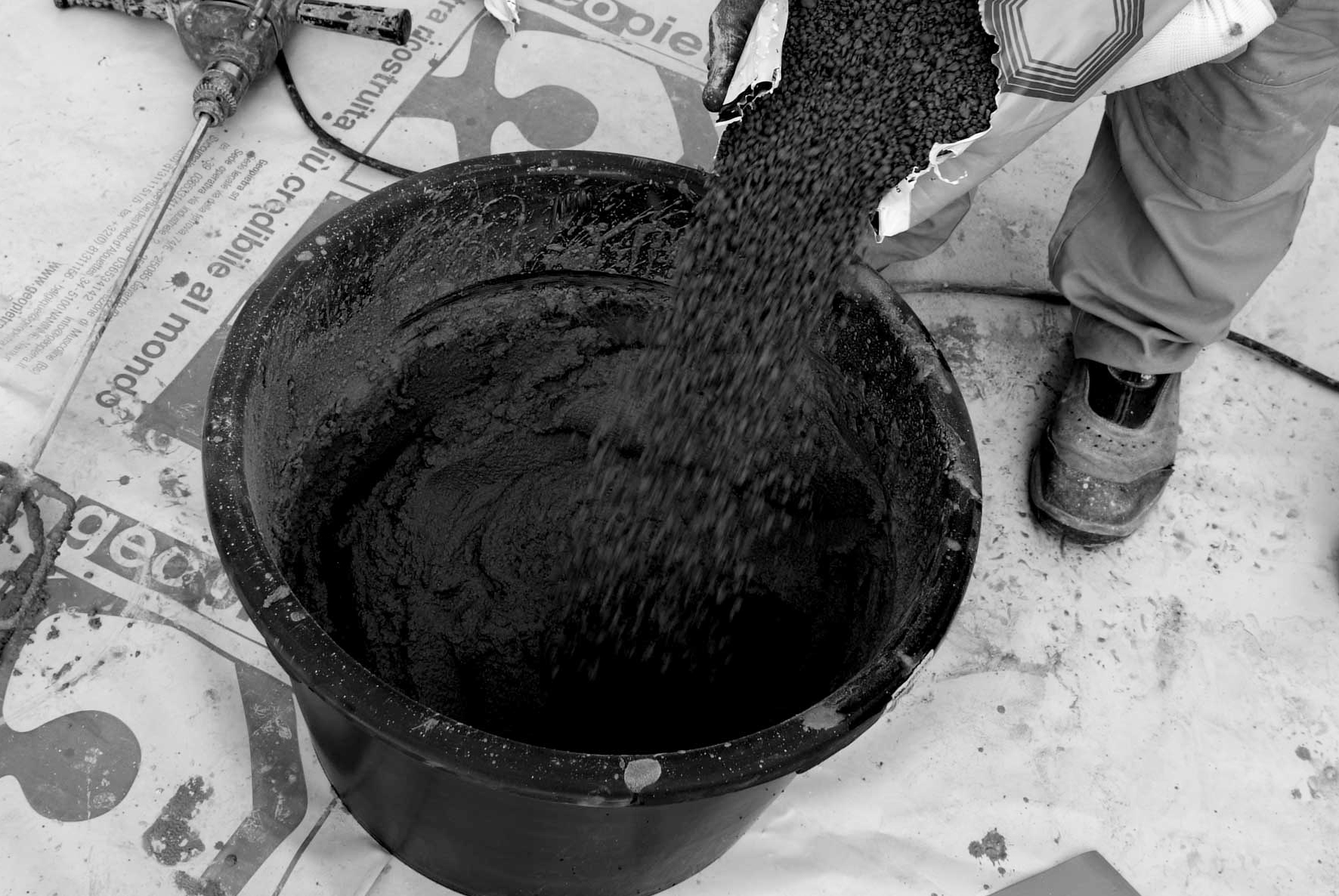

APPLICATION
Cut the nozzle off the piping bag to obtain a suitable hole measuring 1.5-2 cm. Inject the material by keeping the end of the nozzle in the joint, tilting it sideways 45° with respect to the filing direction, and running it along the joint while gradually filling it. The material should always flow easily out of the piping bag without dripping on the stone while injecting. As this is a natural product the colour of the mortar may vary depending on factors such as wind, humidity, temperature and drying times. As a result avoid leaving a wall half grouted (from edge to edge), completing the work in one session. GeoBi can also be used to fill small gaps that occur during installation with half-filled joints.
FINISHING
Wait for the initial application to harden before proceeding with any other intervention. It is safe to proceed when water is no longer released when touching the mortar with a finger, and the material can now be worked using a wooden stick, spatula, glove or trowel, depending on the result required.
N.B. The mortar will mark the stone permanently, therefore keep the surface of the stone clean unless a plaster finish is required.
COLOUR
Pre-mixed coloured powder mortar | 6 colours

GRAIN SIZE
Wet volcanic aggregate | 2 particle sizes
GeoBI F/fine grain (0-3 mm) is recommended for retouching dry-stack installations and finishing the TERRAKOTTA brick slips.
GeoBI G/coarse grain (3-8 mm) is recommended for finishing all manufactured stone veneer profiles.
With the advent of new construction requirements, grouting implemented with sand/cement-based mixes are inadequate. The different weight, breathability and thermal expansion characteristics between mortar and manufactured stone veneer create technical problems, such as the appearance of thermal bridges, excess weight, cracks etc. Thanks to GeoBi, the characteristics of the mortar are similar to those of Geopietra® manufactured stone veneer, standardising the technical characteristics of the finished wall. The wall is lighter, can breathe, and has a uniform composition. GeoBi is therefore essential for installations on wood, insulation, asbestos cement slabs, and all other applications of Geopietra® manufactured stone veneer.
Grouting operations are simplified-joints are easily filled with a piping bag and processing times are reduced. GeoBi widens the possibilities of grout finishes depending on how it is used. Any type of finish can be achieved, ranging from the smoothest through to the roughest, typical of natural mortars. Processing times are crucial when choosing surface roughness requirements.
TECHNICAL ADVANTAGES
- Reduced grout weight.
- Even harmonised wall as it equalizes any thermal expansion of the joint and manufactured stone.
- Reduced thermal conductivity and hence no formation of thermal bridges.
- No risk of cracking as a consequence of shrinkage, which is typical of wide grouting joints.
- Increased breathability of grouting joints.
- Reduced formation of saltpetre from the joints.
AESTHETIC ADVANTAGES
- Due to its versatility, it can be used for any type of finish-from standard to relief-including plastering where grouting plays a major role.
- It gives the joint the rustic charm of old natural mortars with coarse or fine grain finishes.
APPLICATION ADVANTAGES
- Reduced processing time.
- Easy joint filling.